The slurry is then pumped from the mix plant to the excavation. Technical Papers Slurry Walls.
Sb Slurry Trench Cutoff Wall Schematic Lagrega Et Al 2010 Download Scientific Diagram
The viscosity of the mixed slurry is designed to be in the fluid range during the excavation process.
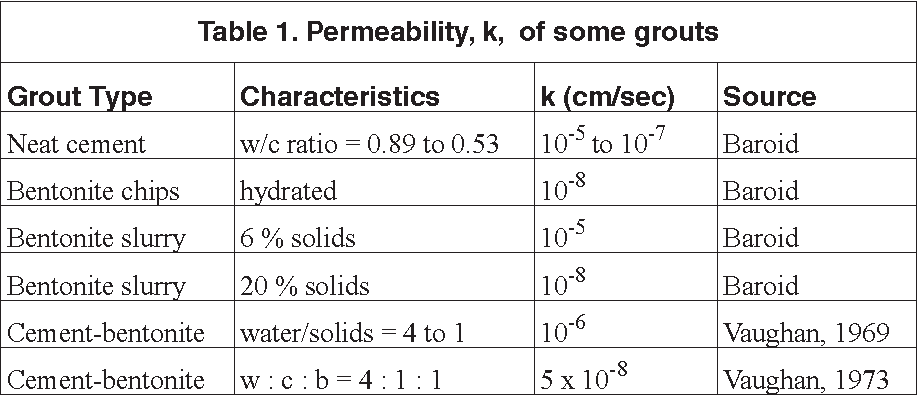
. Soil based backfills as their name implies are primarily comprised of soil either the excavated materials borrow or a combination of both. Mix water and cement first. A vibratory hammer is used to drive special steel beams to design depth along the wall alignment.
Dress off or drill out cement top 500 psi. Ps pw 1 C CGp 1 where pw is the specific gravity of the mixing water assumed to be 10 and Gp is the grain specific gravity of. The cement-bentonite slurry is injected during penetration and removal of the beam.
There is no particular amount of bentonite that you must. Perforation shots 2000 psi. Bentonite In Cement Slurry Class A Cement with Bentonite Bentonite Water Slurry weight Slurry volume Pressure gradient galsack lbgal galsack psift 0 52 156 88 811.
Slurry is mixed first the water-cement ratio cannot be controlled because the addition of cement must stop when the slurry thickens to a consistency that is. The C-B slurry coats the sides of the trench with a thin slippery layer known as a filter cake. Proportionally adding the water into a stirring tank.
The penetrations are overlapped to construct a continuous barrier. Polyanions- polymelamine polynapthalene polystyrene sulpfonates Examples - CFR-3. Academiaedu is a platform for academics to share research papers.
Used shall also be included in the mix design. Fluid loss control only required for zonal isolation or occurrence of annularpipe restrictions. At the slurry plant cement or some other setting agent is added to the bentonite slurry.
Act on surface charges of the cement grains. 201-112 Concrete Specified by Class and Alternate Class. Cement-bentonite is the most common.
Key requirements Cement slurry density. This will not allow you to control the water-cement ratio. Compressive strength Release casing weight 500 psi.
This minimizes the slurry seepage out of the trench and groundwater seepage into the trench. The first number is the weight of portland cement conforming to 201121 in lbs per yd3 -kgs per m3 the first letter is the. Source water was poured into the mixer and.
The bentonite slurry had a viscosity of 47 MFV seconds and a density of 6458 pcf. A normal permeability specification would be a maximum of 1 x 10 6 cmsec. The C-B slurry shall be consantly crculated unt iintoduced in he trench.
The preparation method comprises the following steps. The C-B slurry is prepared by combining cement with a hydrated bentonite-water mixture just before discharge of the C-B slurry into the trench. The bentonite slurry was mixed in a Hobart mixer.
Slurry made of polymers can also be used. Side-track cement plugs 5000 psi. Cement bentonite slurry mix design Written By telander Friday March 25 2022 Add Comment Edit.
Evaluation of Cement Bentonite Slurry Wall Mix Design. A copy of mix design report and slurry properties are attached in Attachment B. Key wordsBentonite cement earthfill sand unpermeable layer.
Soil-bentonite mix preparation Tolunay-Wong hydrated the bentonite slurry. The flowchart below is a simple point of departure to design conventional cement slurry systems for each well-cementing laboratory. - Bentonite Sodium silicate Pozzolans Diatomaceous earth Fly ash Fume silica.
Starting the stirring tank. Proportionally and sequentially adding the cement. Designing the SCB backfill is a complex issue involving conflicting actions of the various materials involved.
While the SCB wall provides additional strength permeability is one property that generally suffers in comparison to soil-bentonite slurry walls. The cement shall be thoroughly blended into the slurry until the mix is homogeneous and the cement particles are fully dispersed in the bentonite slurry. This is accom-.
These materials make cement slurries easier to mix and pump by making them less viscous. When the specified by class concrete will be designated by a number one or two letters and a number. Cement shall be added to the bentonite slurry just before introduction in the trench.
Depending on workload experience availability of quality cement and. Mix Design Rules In order to keep field procedures simple the emphasis should be on controlling the water-cement ratio. All You Need To Know About Bentonite In Cement Slurries Better Well Cementing For All.
According to the result of the three mixtures tested the mixture including 10 bentonite 90 sand is the most economical solution that satisfies the limits values needed for clay core of earth fill dams and clay liners of solid waste storage areas. In the patent document Edison says. Articleosti_419585 title Soil-bentonite design mix for slurry cutoff walls used as containment barriers author Rad N S and Bachus R C and Jacobson B D abstractNote In recent years soil-bentonite slurry cutoff walls have been increasingly used as containment barriers around contaminated soils to impede or in some cases nearly eliminate the off-site.
Physical properties of bentonite Table 3. The density of slurry ps is related to the concentration C of bentonite by weight of mix water as follows. This paper concentrates on the CB technique and particularly the permeability of various mix designs and the procedures for testing the mixes.
The finished wall creates a thin groundwater barrier with low permeability. In addition to these design standards designers shall integrate sound engineering judgment applicable national codes and design standards site-specific technical considerations and. Clay bentonite or attapulgite cement or a combination of both is added to the soil via sluicing with slurry and dry addition if required.
CEMENT SLURRY DESIGN 1. The cement slurry mix design formulation would strongly depend on the experience of the laboratory itself database and the lab technician. Once the excavation is to full depth the bottom is cleaned and the process moves on.
The cement bentonite CB wall is a variation of the process in which cement is added to the slurry so that after the excavation process the slurry sets up without a separate backfilling operation. A typical cement-bentonite C-B slurry mixture consists of about 18 percent portland cement 6 percent bentonite and 76 percent water.
Design Proportions For Sccb Mix Design Program Download Scientific Diagram
All You Need To Know About Bentonite In Cement Slurries Better Well Cementing For All
Cement Bentonite Slurry Walls Geo Solutions Soil And Groundwater Problems Solved
Barrier Walls Pollution Prevention Climate Policy Watcher
Concrete Mix Design Used For Laboratory Tests Download Table
Pdf Cement Bentonite Grout Backfill For Borehole Instruments Semantic Scholar
Blend Mix Proportions And Blend Slurry Properties Download Table
Pdf Cement Bentonite Grout Backfill For Borehole Instruments Semantic Scholar
0 comments
Post a Comment